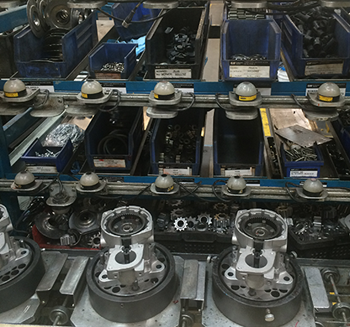
If you have older trucks in your fleet—ones that are outside warranty—you are likely looking for cost-effective ways to handle repairs when they arise. Budget-conscious buyers often look to other non-OE (original equipment) remanufacturers, local rebuilders and coreless whitebox products. While they may be lower priced, these aftermarket options are actually more prone to problems and failure.
“These ‘value’ or offshore products are not made from OE components—or to OE specifications,” explains Brian Koehlinger, Senior Sales Manager. “They use aftermarket parts that are known to be inconsistent and unreliable. You may get a better deal upfront—but chances are you’ll pay for it when your truck is stranded on the side of the road or in the shop again for repairs.”
That’s where the Delco Remy reman product line comes in.
While new service is always the best option, the reman offering is the ideal solution for buyers seeking quality alternators and starters at a lower price than new service. That’s because what happens at our remanufacturing site is quite different—and so is the result. In a dedicated facility, we remanufacture a high volume of alternators and starters each year in a process that’s as methodical as our OE plants. In fact, the link to OE is something that can’t be found in a simple rebuild. Our OE engineers are involved in the remanufacturing process.
“Our reman alternators and starters incorporate OE components, processes, testing and validation—something our competitors can’t offer because they aren’t an OE,” says Mike Kelley, Senior Account Manager - CV Aftermarket. “We integrate the latest changes that happen over a product’s life cycle, so our reman units are always the same generation as the new ones.”
This means variability is not an issue like it is with non-OE versions. The non-OE rebuilts typically don’t know about the latest changes so their versions are not up-to-date—another reason why they are plagued with more reliability issues.
Our Remanufacturing Process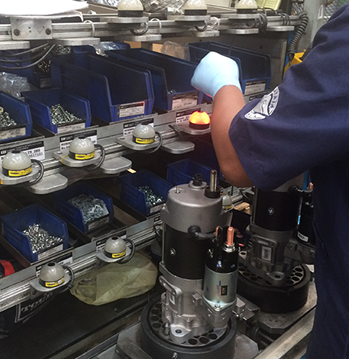
As part of the reman process:
- Components are thoroughly cleaned and some are painted or treated for corrosion resistance.
- Strict procedures dictate inspection of components to ensure they meet OE specifications.
- The product is tested throughout the assembly process and then again after final assembly to ensure quality standards have been met.
- All work instructions and control plans are documented to ensure consistent quality.
- Validation testing is performed on changes made to the product.
The quality workmanship and attention to detail put into our remanufactured products give you a savings where it really counts: dependability, consistency, longer product life, fewer failures, less warranty issues and most of all, more time on the road.
Support You Can Count On
All reman products are fully supported by our customer service, technical support and training teams.
- The customer service team is available to help you with order status and tracking.
- The technical support group provides help with part number applications and troubleshooting for all heavy duty applications.
- We also offer on-site sales and technician training programs.